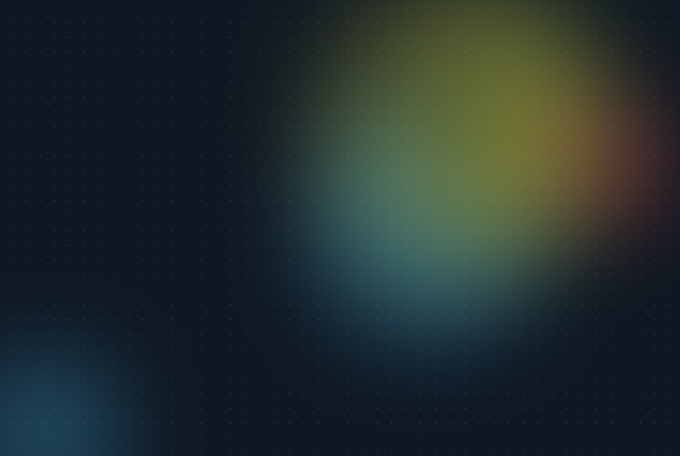
DPSS UV Laser - 355 nm
What do i get here?
The most important facts about DPSS UV lasers for laser marking: Their typical features and key advantages. Insights into the design and main components of a DPSS UV laser at 355 nm. Different laser marking methods and typical materials. Important parameters for choosing the ideal laser source for system integration. Our popular DPSS UV lasers and selection criteria for suitable scan heads. A compact overview of matching beam expanders and F-Theta lenses for professional UV laser marking and engraving at 355 nm.
Features and Advantages of DPSS UV lasers
Our diode-pumped UV lasers with output powers of up to 15 watts at 355 nm impress with their compact design. They can be easily integrated into a wide range of laser marking systems.
At the same time, they offer excellent power stability and outstanding optical characteristics. Ideal for particularly precise and high-contrast marking. Even on challenging materials.
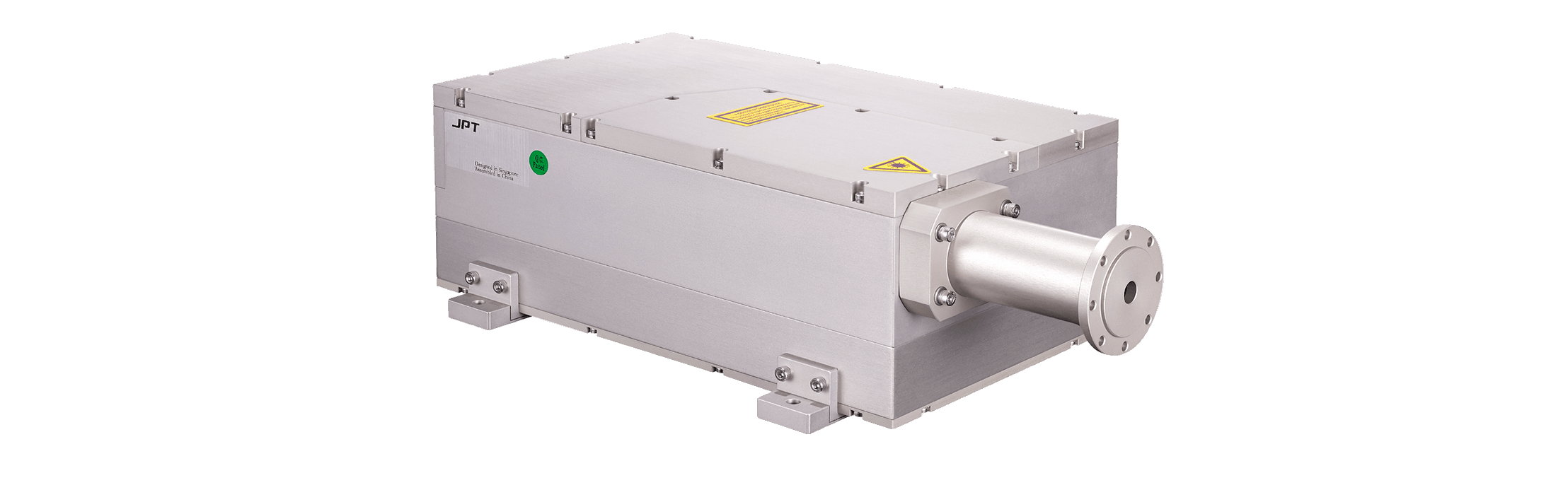
UV lasers at 355 nm are an excellent solution for high-contrast and gentle marking on a wide range of materials such as plastic, glass, stainless steel, copper, ceramics and many more.
They enable permanent, abrasion-resistant and highly visible markings even on challenging materials.
Thanks to their high beam quality and short wavelength of 355 nm, UV lasers offer very fine focus-ability and high power density on the work piece.
Fine details, microscopically small markings or complex patterns can be lasered with outstanding accuracy and precision.
Due to their short wavelength, UV lasers offer the advantage of very low heat input during marking.
This is particularly advantageous when marking thermally sensitive materials or particularly thin coatings.
The lower heat input minimizes the risk of damage, e.g. due to thermal deformation or unintentional colour changes.
Our state-of-the-art DPSS UV lasers are not only known for their compact all-in-one design and low weight, but also for their remarkable versatility.
Their design enables effortless integration into a wide range of industrial laser marking systems, including those with particularly compact dimensions.
Are you looking for further information about our DPSS UV lasers or anything else?
Please let us know.
Typical structure of a DPSS UV laser
The design of a DPSS UV laser, also known as diode-pumped solid-state laser with a wavelength of 355 nm, comprises several essential components that together ensure reliable and precise beam generation.
High-performance pump diodes and active laser crystal
The main components include high-power pump diodes as the energy source and the laser crystal as the active solid-state medium. The pump diode excites the crystal and ensures a population inversion in the laser medium to initially generate and amplify infrared laser radiation.
The reliability and stability of the pump diodes are crucial for the service life and power stability of the entire UV laser source.
Nonlinear crystals for wavelength conversion
Frequency doubling is used to generate the desired ultraviolet laser wavelength of 355 nm.
First, the infrared laser beam is guided through a non-linear crystal, which first converts the laser light into a wavelength close to 532 nm. A second crystal then converts it to the required UV wavelength of 355 nm.
The quality and durability of these crystals are decisive for the efficiency and service life of a UV laser.
Precise control for stability and performance
A high-performance internal control system ensures fast and reliable communication between an external control card and the laser source.
It enables the laser beam to be switched on and off quickly and the laser power, pulse frequency and internal processes of the laser source to be precisely controlled.
The built-in control system is responsible for the reaction behavior and stability of the laser source.
Laser Marking methods with a DPSS UV Laser
Lasers at 355 nm open up a wide range of possibilities for marking various materials. Here are some popular marking methods that can be realized with our DPSS UV laser sources.
Engraving
By precisely removing material layer by layer, a DPSS UV laser can be used to create aesthetic and permanent engravings on a variety of surfaces.
This method enables the permanent marking of metals, plastics, glass, ceramics and other materials.
Even microscopic engravings of just a few µm can be realized with a UV laser.
Laser Engraving: Advantages, challenges and useful tips from our laboratory
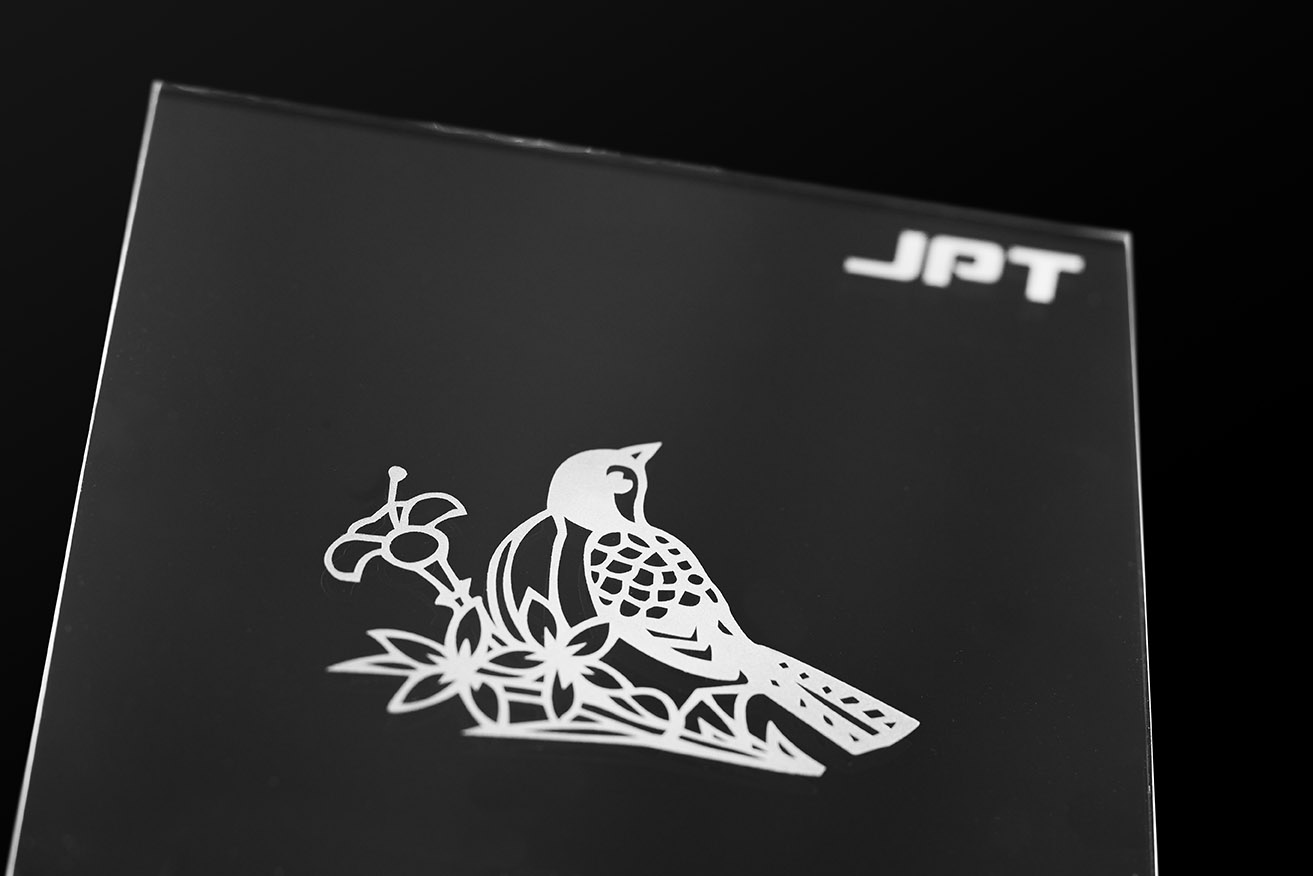
Annealing
A DPSS UV laser can be used for heat-induced marking of metallic materials. The surface is selectively heated by the focused laser beam, resulting in a color change.
This marking method is ideal for ultra-precise and gentle marking on various materials.
Laser Annealing Marking: Advantages, challenges and useful tips from our laboratory
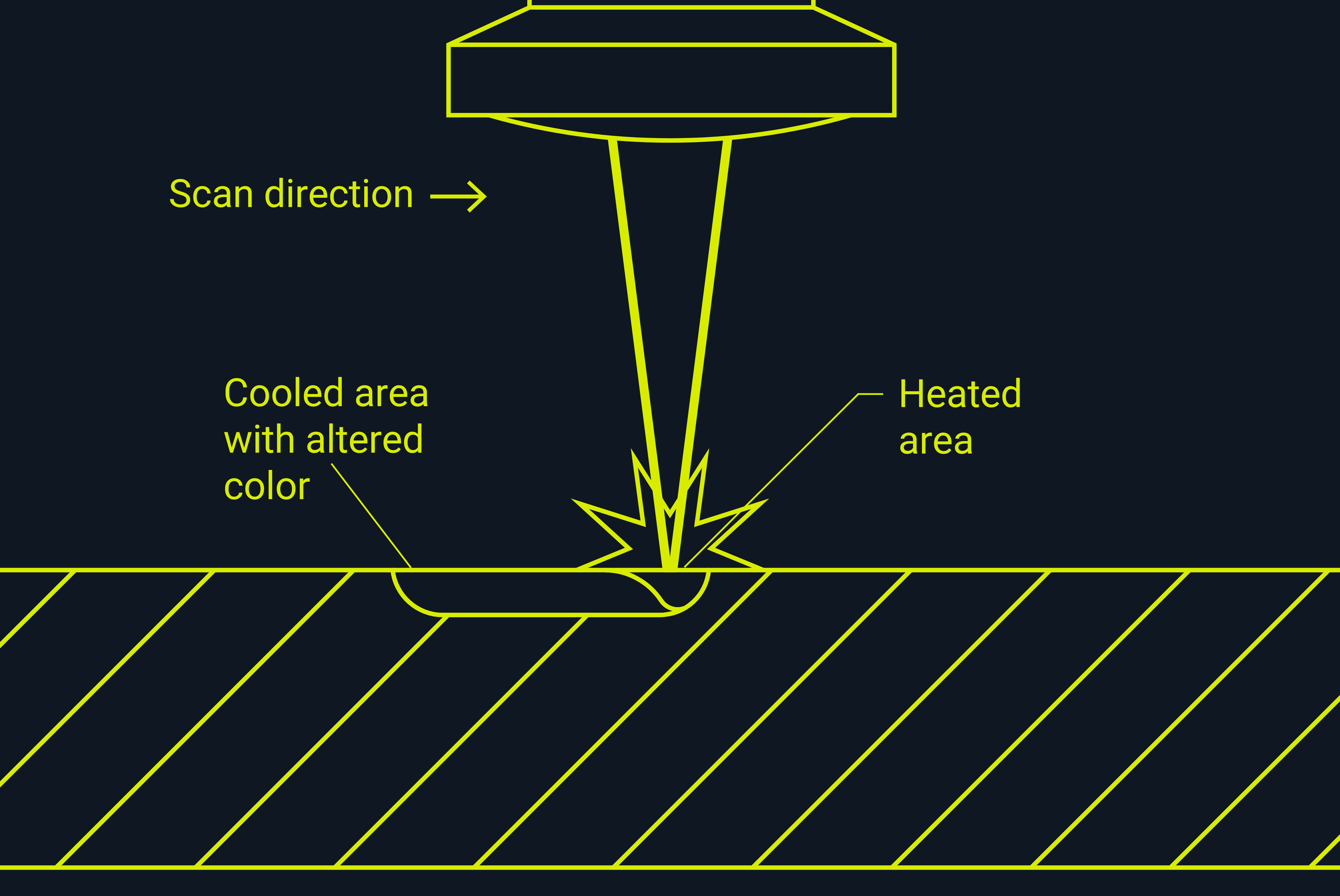
Color Change
By adjusting the process parameters, a UV laser can activate or fade the chemical components of the material and thus cause a color change.
Even many challenging plastics can be marked smoothly
UV lasers are therefore often used in the marking of consumer electronics and white goods.
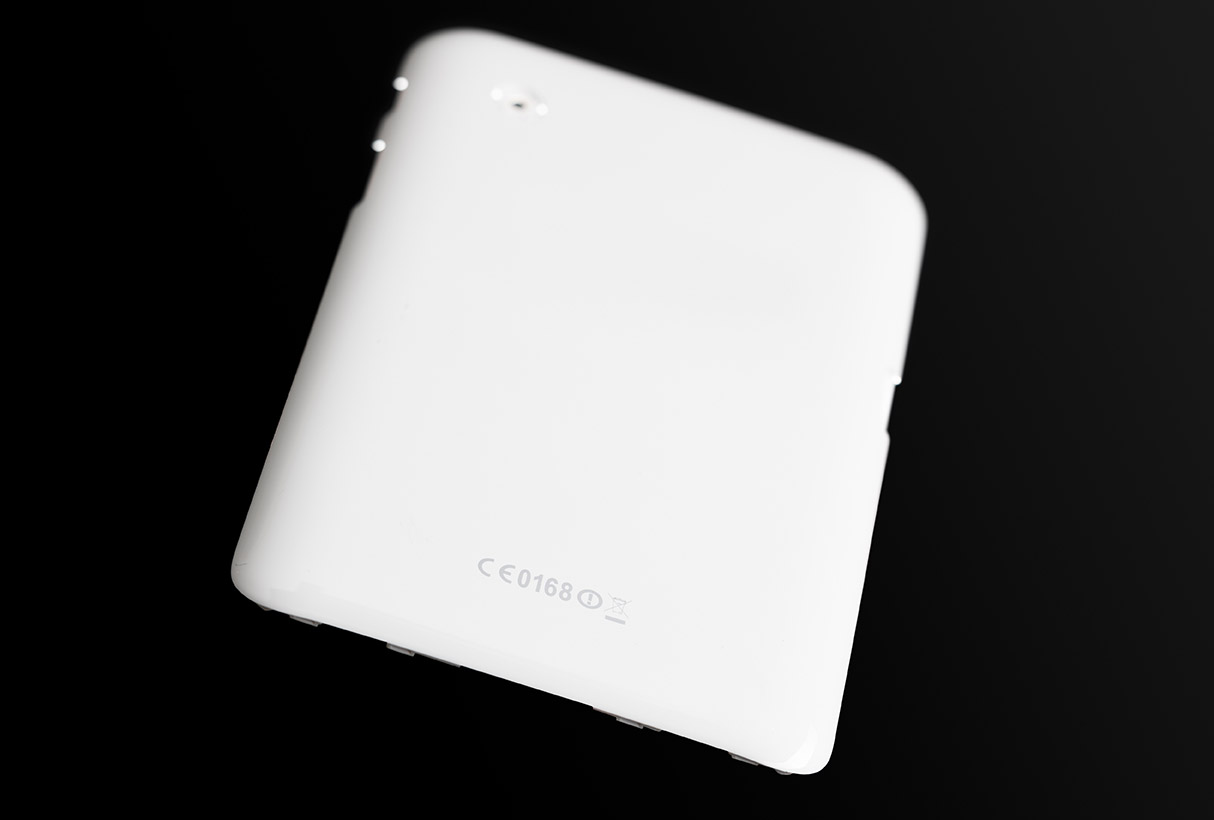
Ablation
Laser ablation marking is a precision process in which the coating material is selectively vaporized on a substrate, creating a clear colour contrast between the coating and the underlying base material.
To further improve visibility, backlighting can be combined with ablation marking.
Laser Ablation Marking: Advantages, challenges and useful tips from our laboratory
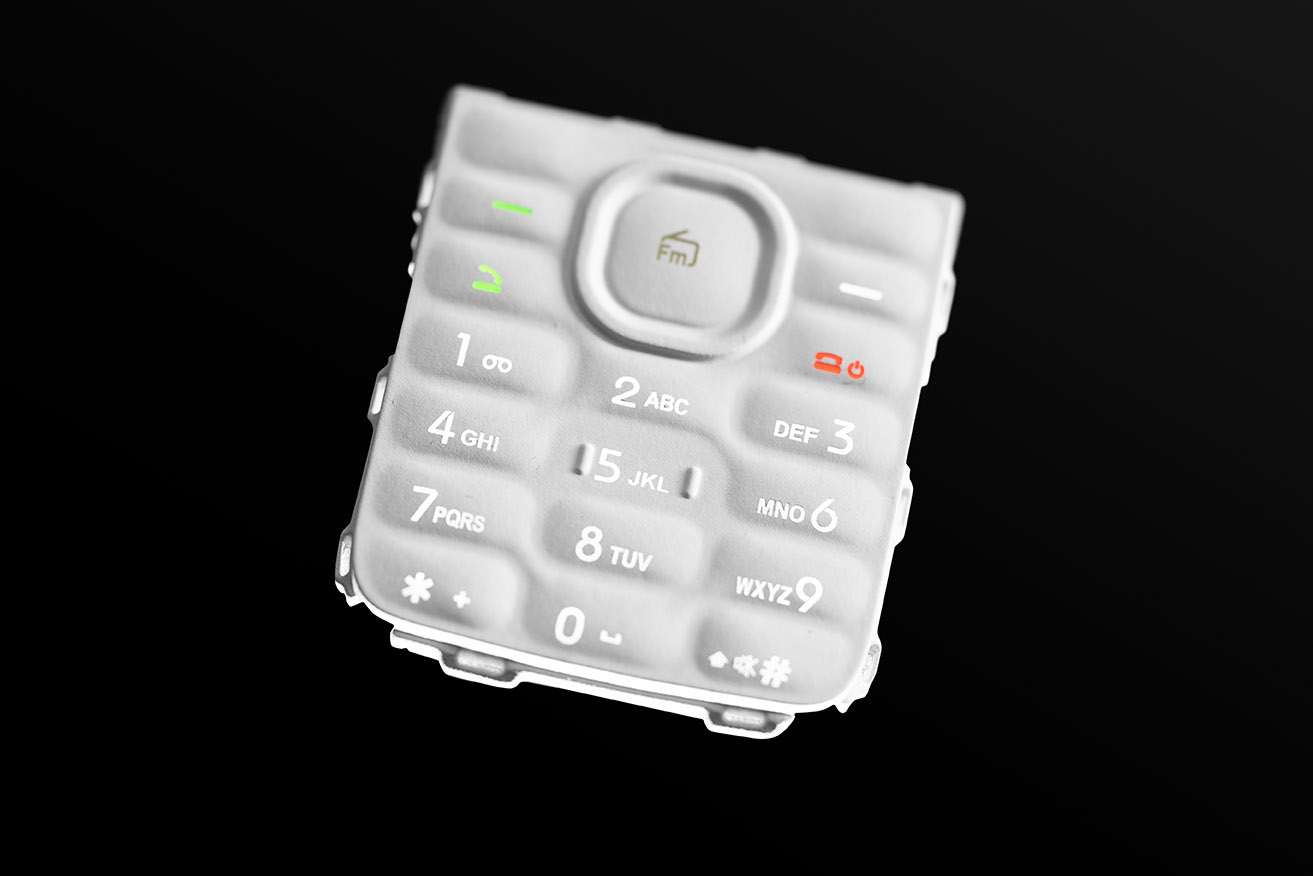
Foaming
By selectively foaming the material with a DPSS UV laser, high-contrast and precise markings can be achieved, particularly suitable for marking plastics and other heat-sensitive materials.
Depending on the selected laser parameters, the controlled, foaming of the material creates optical and, if required, more or less tactile markings on the surface of the workpiece.
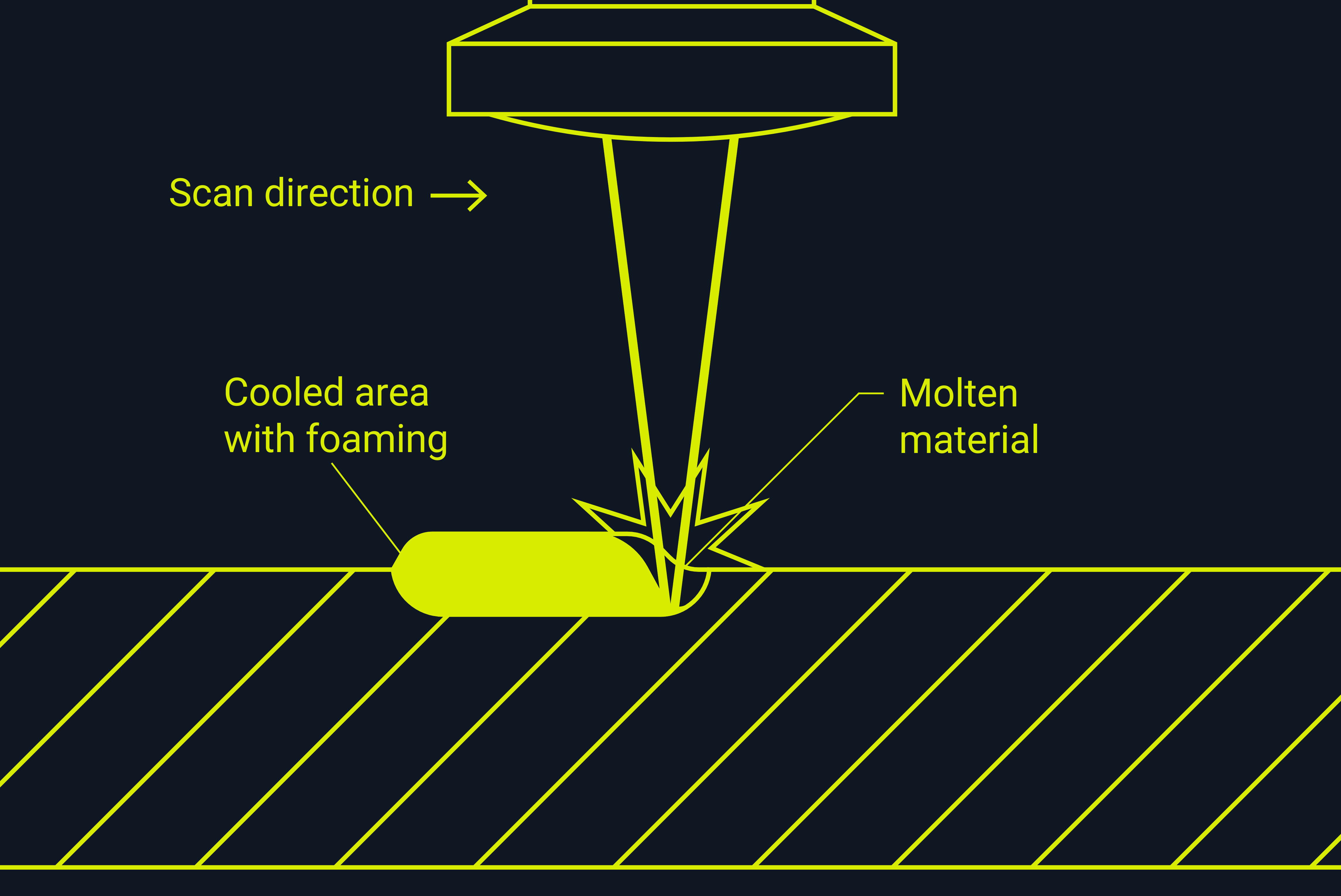
Are you looking for further information on laser marking or other applications done with UV laser sources?
Or would you like to talk to us about any other topic?
Please let us know.
Typical materials for marking with DPSS UV Laser
UV laser sources with a wavelength of 355 nm are ideal for especially precise and gentle laser marking. Even on many challenging or sensitive materials.
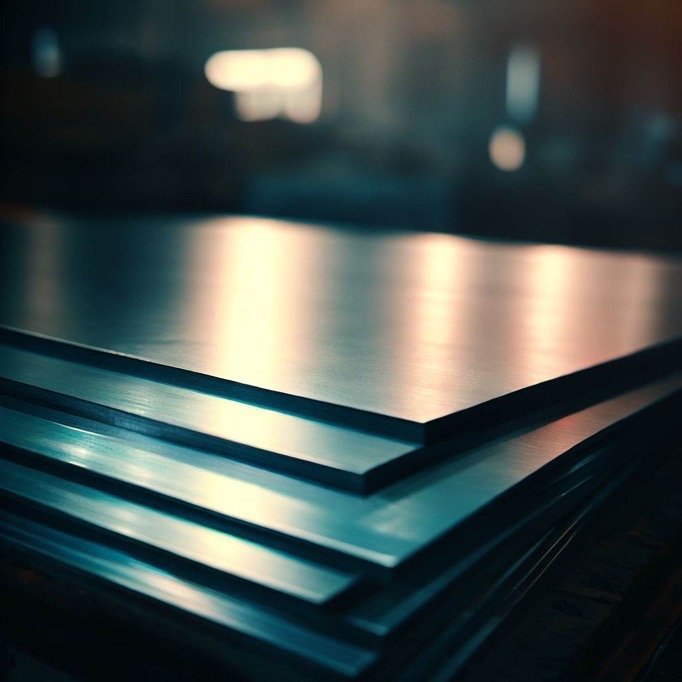
Metals such as stainless steel, aluminum, copper, titanium and brass can be marked permanently and with maximum precision using our UV laser sources.
The fine focus-ability of the ultraviolet wavelength allows particularly high power densities on the material surface and enables clear and permanent markings on the metallic surfaces.
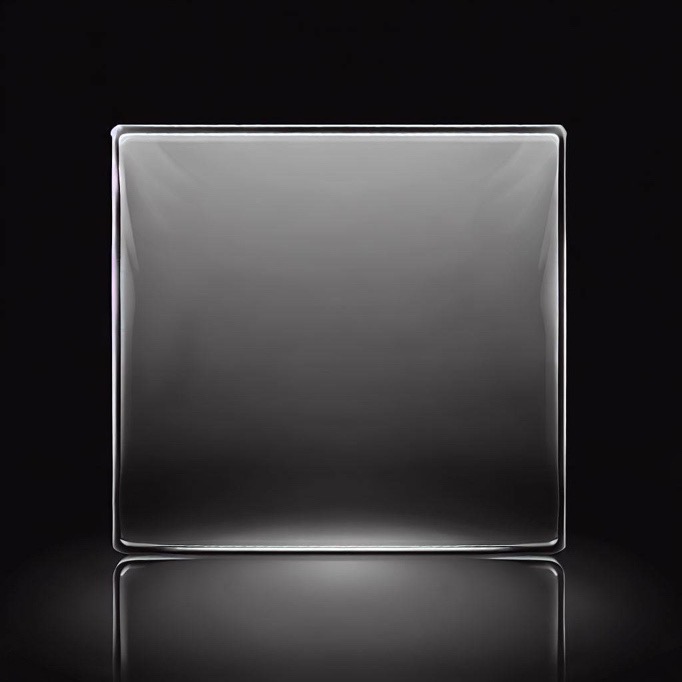
Due to the wavelength of 355 nm, which is very well absorbed by many crystalline materials, and the excellent focus-ability, our DPSS UV laser sources enable extremely small, fine and precise on-glass- or in-glass-marking.
They generate significantly less heat during marking than higher wavelengths, which minimizes the risk of thermal damage to the glass substrate.
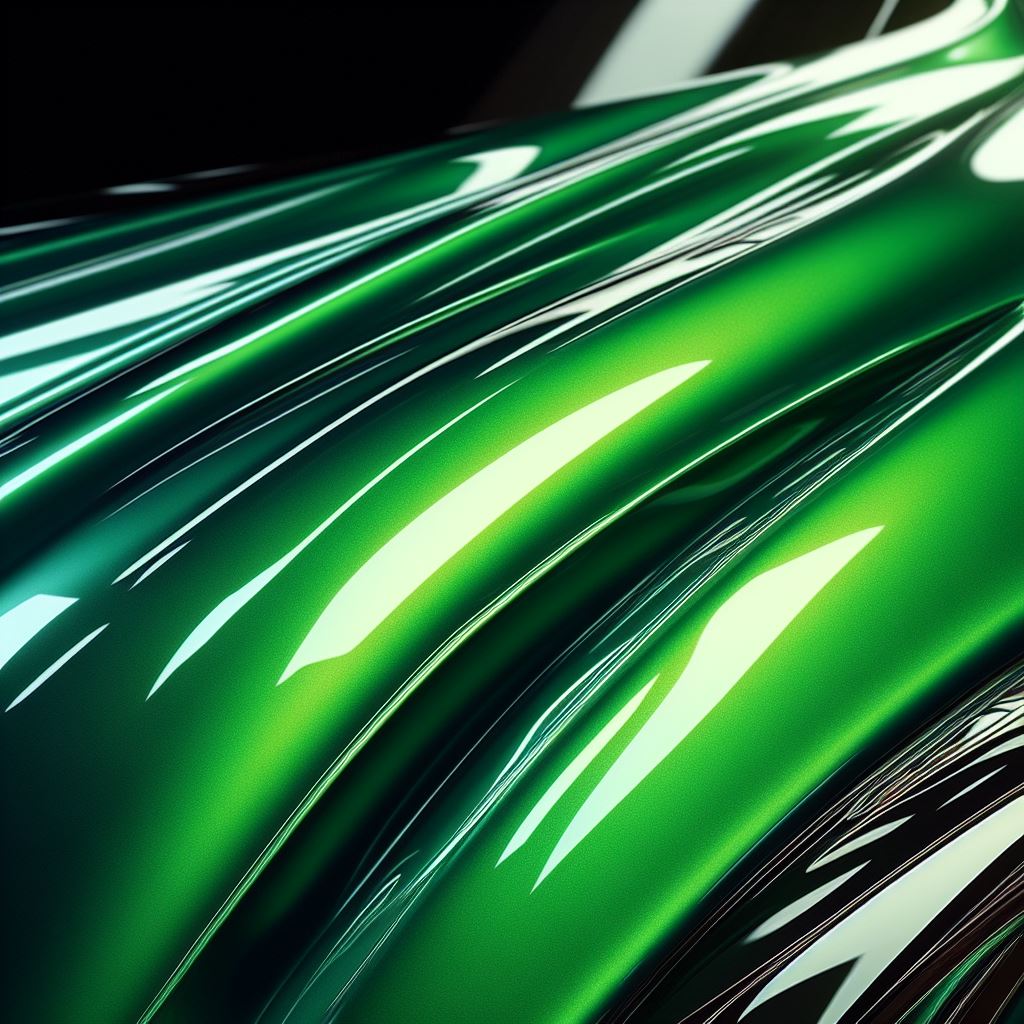
The selective removal, structuring or activation of paint or lacquer layers with the finely focused UV laser beam results in permanent and particularly precise marking.
Even microscopically small markings of just a few micrometers can be applied with outstanding accuracy.
The low thermal impact during marking, reduces the risk of damage to the underlying material.
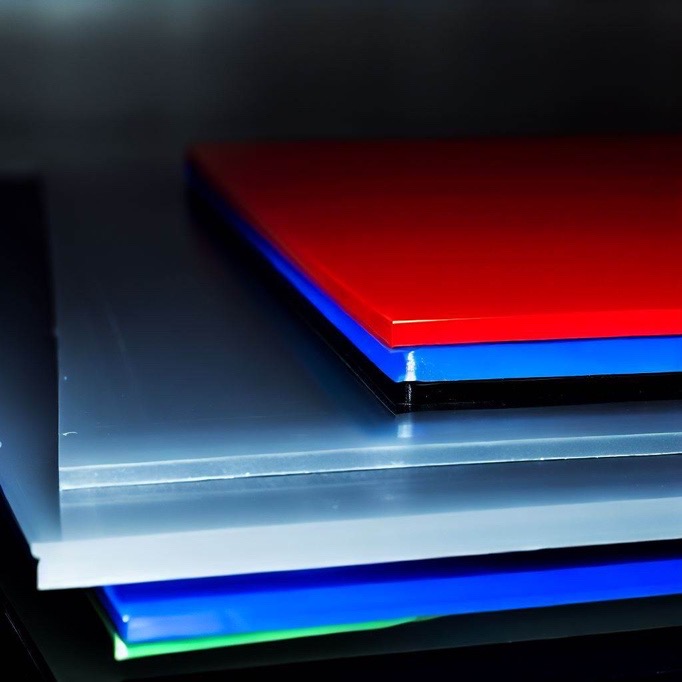
Plastics and polymers such as ABS, PE, PET, PC and PMMA can be marked with a UV laser.
The focused laser beam causes chemical or structural changes to the plastic surface. This results in detailed, high-contrast and permanent markings.
UV lasers offer the advantage of minimal thermal stress. This is particularly advantageous for marking sensitive plastics.
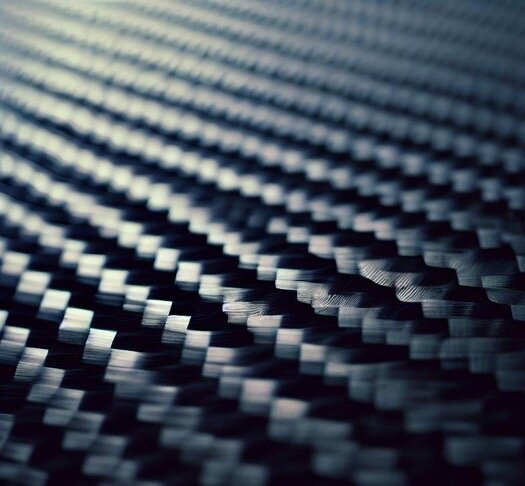
Composite materials such as Kevlar, carbon and glass fiber reinforced plastic (GRP) can be engraved precisely and gently with the UV laser.
The fine focus-ability of the UV laser enables particularly efficient and smooth laser marking, even in microscopic dimensions.
UV lasers also offer the advantage of non-contact processing with minimal thermal stress on the workpiece.
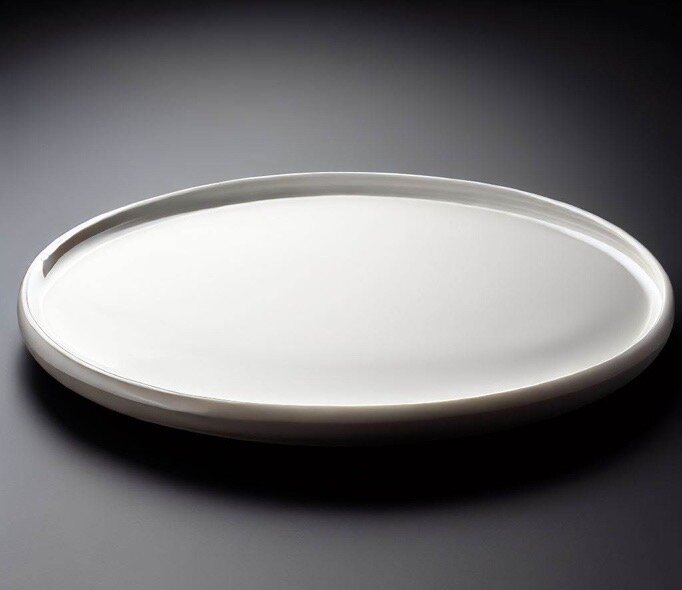
The high power density and wavelength of the focused UV laser beam enable aesthetic, durable, and perfectly visible markings on ceramic surfaces.
Ceramics such as porcelain and stoneware can be marked precisely and with minimal thermal stress. This significantly reduces the risk of cracks or deformation and preserves the properties of the ceramic material.
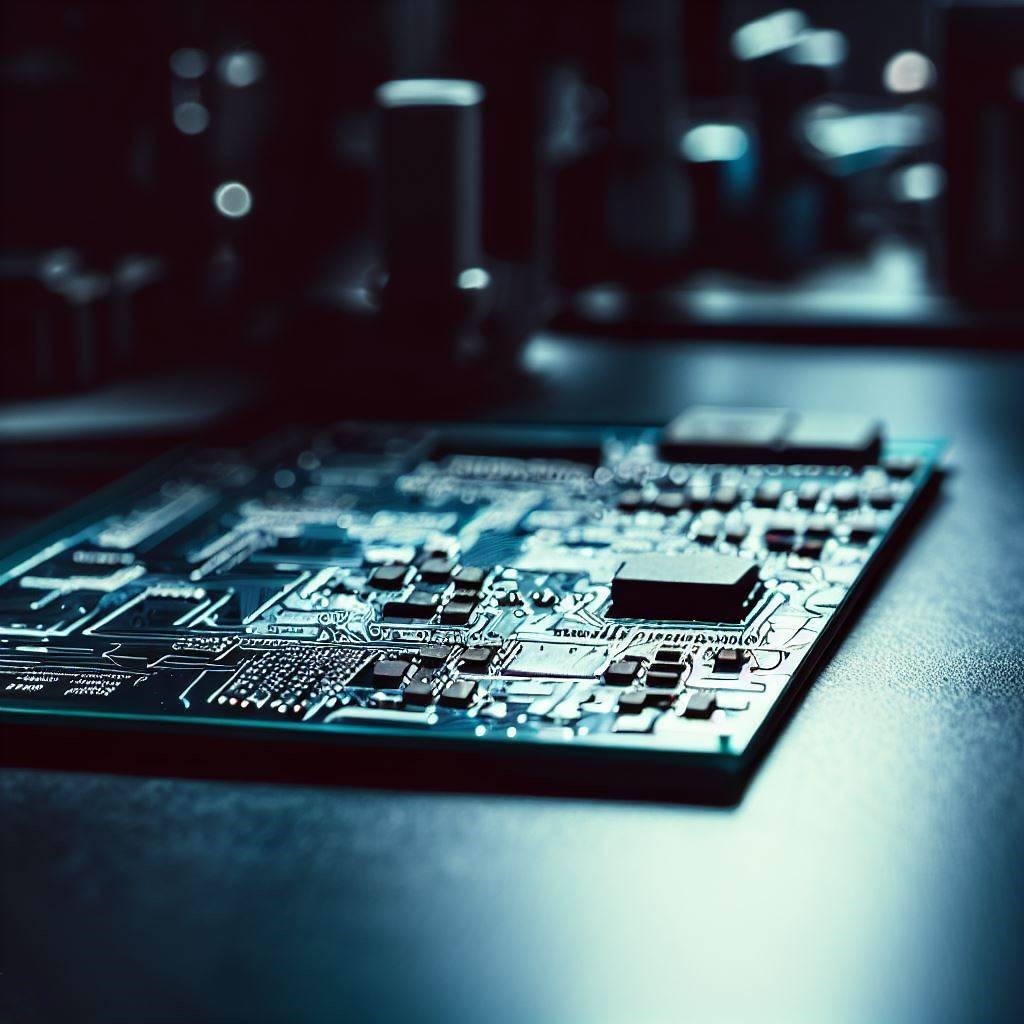
The particularly fine focus-ability of the UV laser beam enables high-precision engraving or marking of semiconductor materials such as silicon and others.
Fine markings in the µm range can be realized reliably.
In addition, the minimal thermal impact of the UV laser reduces the risk of damage to the sensitive semiconductor materials.
Are you looking for information on laser marking other materials with a UV laser?
Or would you like to talk to us about any other topic?
Please let us know.
Laser selection criteria
When selecting a DPSS UV laser source at 355 nm for integration into a laser marking or engraving system, various laser parameters play a decisive role.
Here are the most important ones to consider.
The output power of a laser source specifies the maximum laser power that it can emit at the specified wavelength.
Laser sources with a higher output power can in many cases complete tasks faster than those with a lower output power.
In addition, a higher output power can simplify the processing of denser and harder materials, which expands the range of applications for a laser system.
The pulse frequency range indicates how often the laser can emit pulses per second. In most cases, higher pulse frequencies enable faster processing and therefore greater throughput and efficiency for industrial material marking.
For diode-pumped solid-state lasers, the optimum pulse frequency for achieving the maximum laser output power is typically fixed and is specified in the technical information.
The maximum pulse energy indicates how much energy the laser can emit per pulse.
A higher maximum pulse energy enables more aggressive material removal. This is particularly helpful for applications that require deep material engraving.
Additionally, a higher maximum pulse energy expands the ability to engrave a wider range of materials. Including those with higher density or hardness.
The pulse width and pulse peak power characterize the duration and intensity of a laser pulse.
Short pulse widths and high peak powers of DPSS UV laser sources reduce the heat input during laser marking.
They allow better control over the heat affected zone of the laser marking or laser engraving.
The beam quality M² is a key figure that describes the quality of a laser beam. It indicates how close a laser beam comes to an ideal, divergence-free beam.
The lower the M² value, the better the beam quality and the focus-ability of the laser.
Our DPSS UV lasers offer excellent beam quality in combination with the short wavelength of 355 nm. Using a suitable F-Theta lens, this results in extremely fine focus diameters of just a few micrometers.
Popular DPSS UV lasers for laser marking
Here you can find our popular DPSS UV laser sources for system integration and especially precise, material-friendly and versatile laser marking at 355 nm.
Are you looking for a UV laser source for your system integration or process development?
Or would you like to talk to us about any other topic?
Please let us know.
Choosing a scan head for DPSS UV lasers
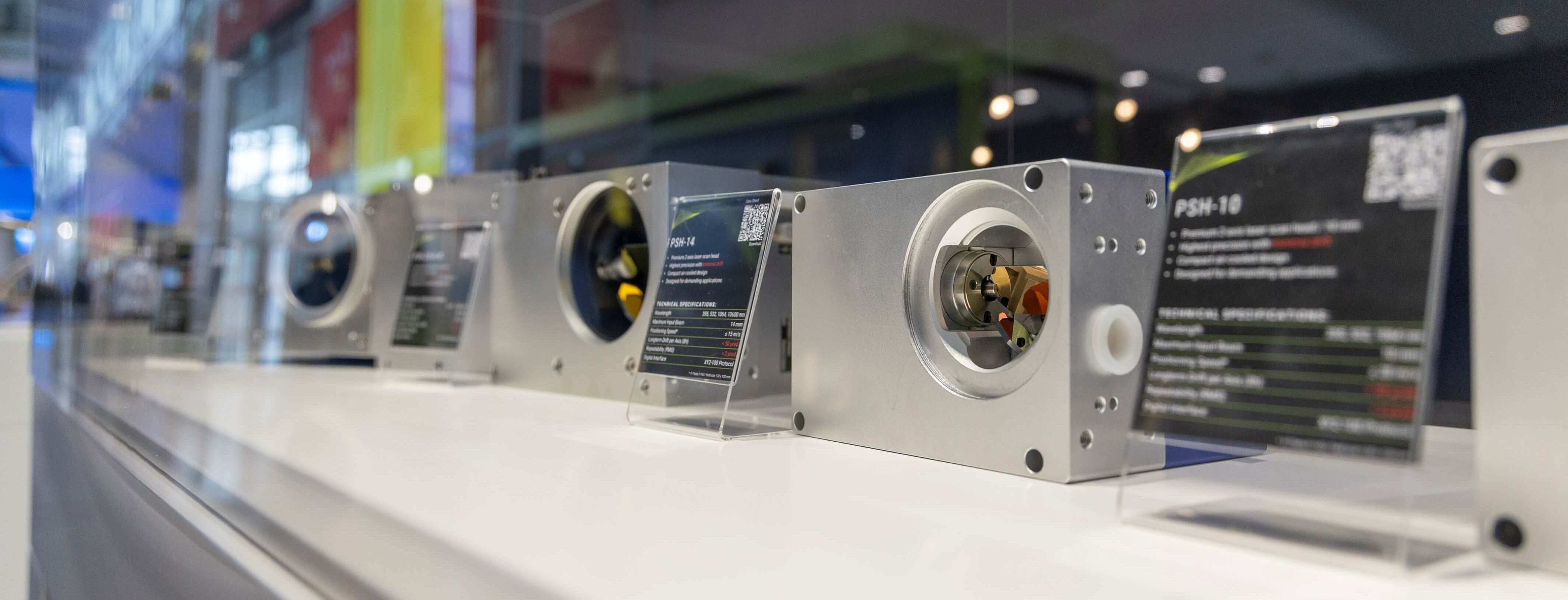
When choosing a scan head, it is essential to carefully consider factors such as the coating of the deflection mirrors, power compatibility, mirror size, and existing requirements in terms of precision and process speed.
Used Wavelength
The coating of the deflection mirrors should be precisely matched to the wavelength of the laser.
This ensures optimum reflection of the laser beam and prevents absorption of laser power that could damage the coating or mirror.
Careful consideration of wavelength compatibility is of major importance.
Maximum Laser Power
The power compatibility of the deflection mirrors plays an important role.
Larger deflection mirrors can typically handle more laser power, as the power density on the coating decreases when the laser beam is expanded to match the larger mirror size.
This reduces the risk of damage and ensures the accuracy and longevity of the laser deflection unit.
Beam Diameter
The diameter of the laser beam is inversely proportional to the focus size on the material.
An initially larger beam diameter allows for finer focusing, resulting in higher power density and more precise marking.
It is important to consider the diameter of the laser beam when selecting the deflection unit to ensure that the mirror surfaces are optimally utilized and no laser power is cut off by the scan head.
Process-Requirements
When choosing a scan head for system integration or process development, it is crucial to anticipate future needs for accuracy and speed in the intended application, alongside considering the size, weight, mountings and interfaces of the scan head for seamless integration.
For precision-critical tasks, the use of laser scanning heads with high repeatability, position stability and minimal drift is recommended.
matching optics for DPSS UV lasers
Here you can find all our F-Theta lenses and beam expanders for the wavelength of 355 nm. Suitable for combination with DPSS UV laser sources.
We would be happy to support you in selecting the right model for your system integration.
Are you looking for further information about our F-Theta lenses or beam expanders for laser marking at 355 nm?
Or would you like to talk to us about another topic?
Please let us know.